Adapted from a presentation by George Pedersen.
OVERVIEW
This paper provides substantiation that continuous monitoring and proper management will enable meeting and possibly exceeding the projected life for Valve Regulated Lead Acid (VRLA) batteries, and will improve the reliability of the battery power during a disruption of normal AC power supply. In the context of this article a battery unit is a container in which one or more cells are connected in series to provide a specific voltage on two terminals. A battery system is a string of multiple battery units connected in series to achieve an even higher voltage.
This article reviews and discusses a number of specific items pertinent to the management of a battery system and its associated units. First, we will review a paper by MGE UPS Systems that among other things provides data on over 8,000 battery system service calls. Second, we examine the basis and methods used by the battery manufacturers to arrive at their battery-life predictions, and we will compare the timing of these MGE reported failures with the industry’s anticipated failure pattern. Third, we will review BTECH’s historical battery monitoring data to substantiate the hypothesis that the early detection and replacement of failing units will potentially ensure that a battery will meet or exceed the manufacturers’ specified life. Fourth, we will discuss the expense of replacing batteries on a scheduled basis rather than actively managing them through a comprehensive battery management program.
Specific examples are provided to compare and contrast the behavior of two similar battery strings and the impact on the life of the battery based on how the two users responded to information provided by the battery monitor. This information provides further proof for the reliability of using battery monitors to extend the life-cycle. Charts are included of actual data collected, to allow the reader to understand the technical conditions of the battery systems during specific events or conditions.
Understanding Projected Battery Life versus Reality
In a paper presented at the INTELEC conference in 1997, engineers at MGE UPS Systems introduced the concept of intermittent charging as a means to extend battery life. To compensate for self-discharge, a continuous float voltage is required to maintain the battery at full charge. But, that voltage is also responsible for positive plate corrosion which is the controlling factor in the life of a lead acid battery. The authors predicted that if the battery was allowed to rest for short periods without the voltage applied, then the cumulative rest periods would limit the corrosion and represent a potential extension of battery life. As part of the presentation to support the need for an alternative charging regime they presented data which was derived from more than 8,000 service records. This data showed that the failed batteries had average age of about 3.5 years rather than 5 years as could have been expected based on manufacturer stated expected life and the anticipated failure pattern. The researchers determined that 80% of these failures were due accelerated positive grid corrosion as the result of overcharging.
Lead acid batteries have a finite life due to positive grid corrosion even when operated under ideal conditions. Based on the rate at which that corrosion occurs within a specific battery design, the manufacturer predicts the number of years that the battery will operate before the corrosion impacts its capability to meet specification. To validate these predictions battery manufacturers conduct accelerated life testing using an elevated temperature regime to speed up the corrosion process and reduce the time required for testing.
Although positive plate growth is the accepted failure mechanism under ideal conditions, there are many other conditions that can shorten the life of the battery. These include manufacturing defects, the aforementioned overcharging and undercharging, repeated discharges and the depth of these discharges. Temperature can also reduce life. Operating the battery at 10°C above the nominal operating temperature of 25°C will half its life. These factors can be reduced or even eliminated by utilizing a battery monitoring system to measure, record and report on these critical operating parameters and provide notification of problems that need to be corrected in a timely manner.
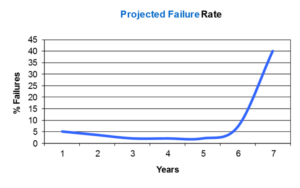
FIGURE 1: Projected Life of a VRLA Battery
This does not mean that if the battery is operating under ideal conditions it will always achieve the battery manufacturers’ predicted life. Like all industrial products the battery is subject to defects introduced during the manufacturing, delivery and installation process. The pattern for all failures follows the generally accepted curve as shown in Figure 1.
Figure 1 shows the expected infant mortality period and a much longer period in which the failure rate is expected to be relatively constant at <2%. This is effectively the useful life of the battery leading to the period near the end of life when the number of failures increases substantially as the battery starts to deteriorate.
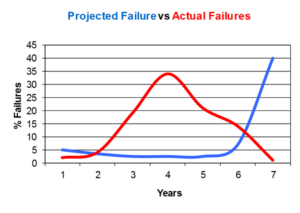
FIGURE 2: Projected failure rate versus actual rate in MGE study
However, when the MGE data from their paper is superimposed on the expected cumulative failure curve as shown in Figure 2, there is a significant difference in the actual failure age versus the expected. This shows the critical need for monitoring the operational parameters of a battery system and the possible detrimental impact on battery unit life if improper conditions are not corrected.
BTECH’S HISTORICAL DATA ANALYSIS
In this section we will examine the hypothesis that battery life can be reduced by neglecting to replace failed battery units. Based on a thorough review of BTECH’s archive of battery monitoring data, we will substantiate the potential to increase battery life when continuous monitoring is in place and the appropriate corrective action is taken. Three examples will be presented, with associated lessons learned.
EXAMPLE 1
The two graphs within this example demonstrate the importance of a commissioning discharge for all new battery systems to help identify units that will fail under the classification of infant mortality.
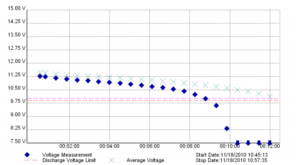
FIGURE 3: New battery unit with low capacity during discharge
The discharge graph for the unit in Figure 3 (blue diamond) shows that it was below the average voltage of all the other units in the string from the start of the discharge (as shown by the green crosses on the graph). The deviation from the average continued to increase until it fell off rapidly nine minutes into the twelve minute scheduled discharge. This is indicative of a unit that does not have the capacity of the other units in the string and the unit should be replaced. In the initial impedance collected before the discharge this unit was higher than the average which indicated a potential problem that was confirmed by the discharge.
The discharge graph of the unit in Figure 4 initially tracked the average voltage of the other units before it failed with a sharp drop in voltage. This is indicative of a unit that probably had internal structural problems, as it would appear that at least one cell shorted after it had been placed under load for a short period. In this case the initial voltage and impedance readings gave no indication of possible problems.
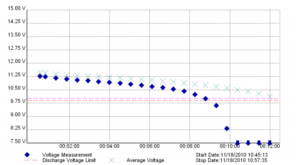
FIGURE 4: New battery unit with a shorted cell during the initial discharge
The battery system from which this data was extracted consisted of five battery strings with 40 units in each string. In addition to the two units shown in Figures 3 and 4, an additional four units within other strings fell below the low voltage threshold. Yet, the battery system as an integrated unit met the required run time. Simply relying on the overall system voltage during a discharge will not indicate that individual units may have failed during the discharge. The units must also be monitored over time to detect developing problems.
EXAMPLE 2
This user had a large UPS system with two strings of 40 12V units. In this case the battery system was actually a replacement for an existing system that had been identified as having failed when the BTECH monitor was installed. The replacement battery was installed in October of 2008 but, as is quite common with battery replacements on operational sites, no commissioning discharge was performed.
Figure 5 shows the average impedance of all the battery units (in green) and is overlaid with the value of the unit with the maximum impedance (in orange).
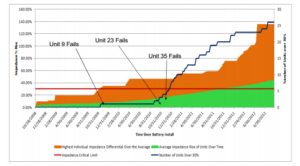
The first unit to exceed the 30% impedance limit occurred one year after the battery was installed, but was not replaced. A second unit exceeded the limit 10 months later and was not replaced, at which point the rate of failures increased until three years and eight months after the battery was installed. In total, twenty-six units exceeded the 30% limit.
During this period, the battery was also inspected quarterly by the UPS service company who consistently advised the customer that there were no problems with the units that were reported by the BTECH battery monitor as being above the 30% critical impedance limit. In July of 2012, the UPS service company identified three units that exceeded their limits (out of the total of 26) and replaced them. They then conducted a discharge test to verify the battery operation.
Figure 6 demonstrates the results of that test. String 1 failed after twenty-nine seconds placing the full load on String 2 which then deteriorated rapidly and collapsed completely after only one minute and fifteen seconds.
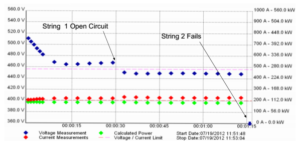
FIGURE 6: Battery voltage during discharge with failed cells
Continuous battery monitoring with a review of the gathered data will identify batteries that could fail. In this case ignoring these warnings subsequently resulted in not only the first battery string failure but also the rapid failure of String 2. Those string failures and load loss could have been avoided by using the battery monitoring information provided to identify and replace all of the failing battery units.
EXAMPLE 3
Like the system in Example 2, this user had a UPS system with two strings of 40 12V units. The battery monitor was installed a short time after the battery was installed and there was no initial discharge data available. The BTECH monitoring system had the impedance alarms set for a 30% rise over the initial impedances recorded.
The graph in Figure 7 shows the average impedance of all the battery units (in green) and is overlaid with the value of the unit with the maximum impedance (in orange).
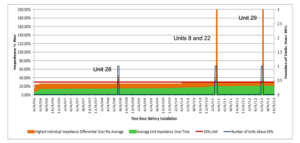
FIGURE 7: Average and maximum impedance values over a 6-year period, including number of failed units
In mid-2008 unit 28 in string 1 of this battery system exceeded the 30% limit and was replaced. The failure of this unit is linked to a power failure on 4/3/2008. During that discharge, unit 28 initially followed the average discharge voltage curve but after five minutes, it started to collapse rapidly. See Figure 8.
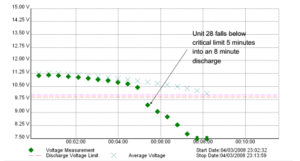
FIGURE 8: Unit 28 voltage during a power failure on 4/3/2008
When power was restored and the battery was recharged, the impedance stabilized for a number of weeks and then began to rise steadily. The unit was subsequently replaced three months later (See Figure 9). The yellow bars indicate the unit has exceeded maintenance limits and is nearing critical limits, and the red bars indicate the unit has exceeded critical limits and will completely fail in the next few weeks.
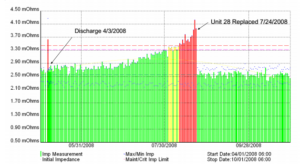
FIGURE 9: Unit 28 impedance rise after the discharge on 4/3/2008
After an additional 18 months in service, 3 additional units exceeded the critical impedance limit and were promptly changed. This battery survived for six years and only four units (out of 80) have been changed. Both the Maximum and Average plots in Figure 5 show a rise in overall impedance with at least one or more units approaching the 30% limit.
Discharge testing without unit level monitoring can be misleading. As indicated, unit 28 fell below the average cell voltage of the string after five minutes into an eight minute discharge, yet the overall string voltage remained at acceptable levels. Without continuous unit level monitoring one would not have identified the under-performing unit voltage relative to other units in the string.
The discharge also demonstrates the potential for a discharge to accelerate or possibly initiate the failure of a battery unit. While the capacity of unit 28 was much less than the other units during the discharge, the battery did support the load. However, the rapid increase in impedance over subsequent months indicated a battery that could now fail on a subsequent discharge if it was not replaced. This confirms that a discharge test only validates the condition of the battery at that moment in time and is not a predictor of future performance.
Continuous battery monitoring with a review of the gathered data successfully identified weak battery units. Weak units were immediately replaced, and, as a result, the battery has exceeded the manufacturer’s predicted life. It also demonstrates that any discharge during a batteries life can negatively affect battery health.
DISCUSSION
Despite the manufacturers’ warranties and service life ratings, batteries can fail prematurely. BTECH’s Battery Monitoring Systems can detect, identify and notify the user of these premature failures. Identifying and taking corrective action – whether it is a failed battery unit or improper operational parameters (over/undercharging, temperature) – will enable the user to maximize the operational life of the battery system.
CONCLUSIONS
-
Early identification and replacement of failing battery units is a viable means of extending battery system life.
-
Replacing all battery units on such a schedule introduces two impacts. First, not all units deteriorate at the same rate. Therefore, battery units with a significant remaining useful life are replaced. This adds unnecessary expense to the operation of the battery system. Second, the risk of battery unit failures in a full string replacement is not completely eliminated because infant mortality will occur in a percentage of those units.
BIBILOGRAPHY
Gun, Jean-Paul, Jean-Noel Fiorina, Michel Fraise, and Henri Mabboux, “Increasing UPS Battery Life,”
R&D Advanced Technologies Team, MGE UPS SYSTEMS, INTELEC, 1997.